Picture |
Description |
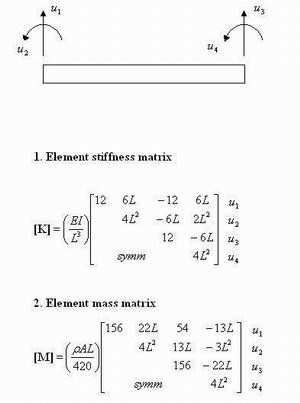 |
CRS = Critical Rotational Speed. When the shaft
is spinning we don't wish the system be resonant at any natural frequencies.
This can be done by limiting the rotational speed lower than system's lowest
natural frequency. We of course can utilize any commercial finite
element codes to solve it, but they are large ,expensive and complicated not
suitable for home builders. A special program like what we are doing might
be quite nice. We start the formulation
by this 2D beam element. Only the first
mode (bending mode) is important, so axial degree of freedom will not be
considered. |
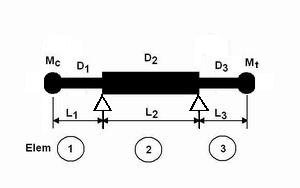 |
Divide the whole shaft into three beam elements.
Mass of compressor and turbine wheel indicated as Mc and Mt respectively. |
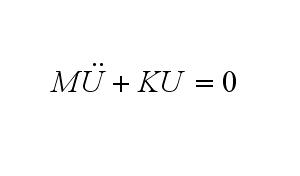 |
Assembling each element's mass matrix and
stiffness matrix, we get M and K. The free vibration problem now has the
form shown left. We have 8 DOFs, two of which constrained. so the final size
of U is 6 DOFs only. 6 DOF is complicated enough for hand calculation. |
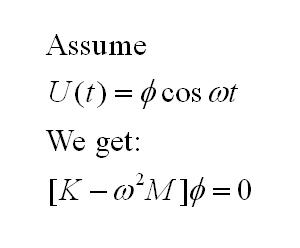 |
To solve the system equation, we transform it
into generalized form of eigenproblem.
|
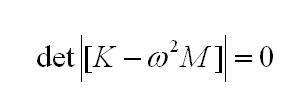 |
Let the determinant of the system equation be
zero we can solve for lowest ω
(unit = rad/sec). However this takes hand
calculation and is extremely lengthy and difficult.
This is how we calculate the critical rotational
speed. What we'll do is to use numerical methods such as Rayleigh-Ritz subspace iteration method
or Generalized Jacobi method instead, to find the natural frequencies and mode shapes. If you are
interested in these methods, please find them in many Finite Element textbooks. |
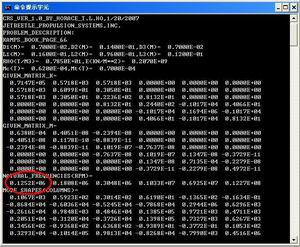 |
Here is a sample of program output.
We reanalysis the natural frequency of Kamps'
book page 66. Click to see larger picture.
it shows ours is 125,200 rpm and Kamps'
136,270 rpm. The maximum design speed was 105,000rpm so it is safe. It is
very interesting that our result is the lower bound of Kamps'.
|
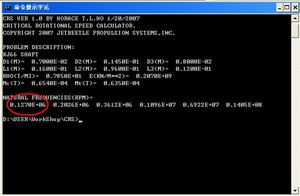 |
Another sample of program output. Click to see
larger picture.
KJ66 is a famous engine now we are able to check
the critical rotational speed in just a minute. We minimize the program
output for brevity. Our program shows 127Krpm,
it is very reasonable because the max rpm of KJ66 was set at 117K rpm. |
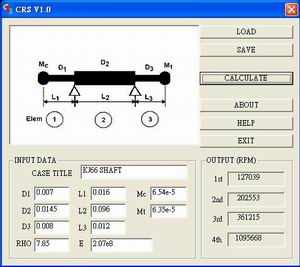 |
This is our user interface looks
like. A lot of coding works but finally done. We will extend this program to
allow more shaft configurations, your help in funding us is highly
appreciated. We successfully
integrated Fortran and C++ so that the user interface and numerical core are
seamlessly working together. |
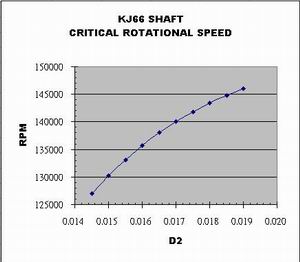 |
Now we have a new toy to play around. Again the
shaft being analyzed is KJ66, we choose D2 as parameter to study. We enter
different D2 values starting from 0.0145, increments 0.0005 each time and
collect the CRS output values, we get this chart. It shows that if we'd like
kj66 to run at higher rpms and thus higher thrusts, we can change D2 to
Φ0.017m or Φ17mm. Shaft tunnel must be changed too. This program is of
thousands of dollars of value ! Should I give it out for free ? |
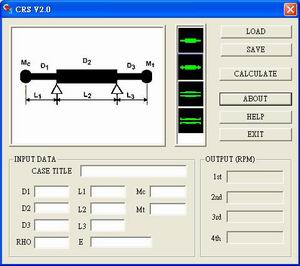 |
CRS V2.0 is under development. This is probably our user interface
will be looks
like. As you can see the shafts available are more than one. A List box is
shown in the middle so user can pick the shaft they want to do the analysis. |